X-RAY CT XT H 450
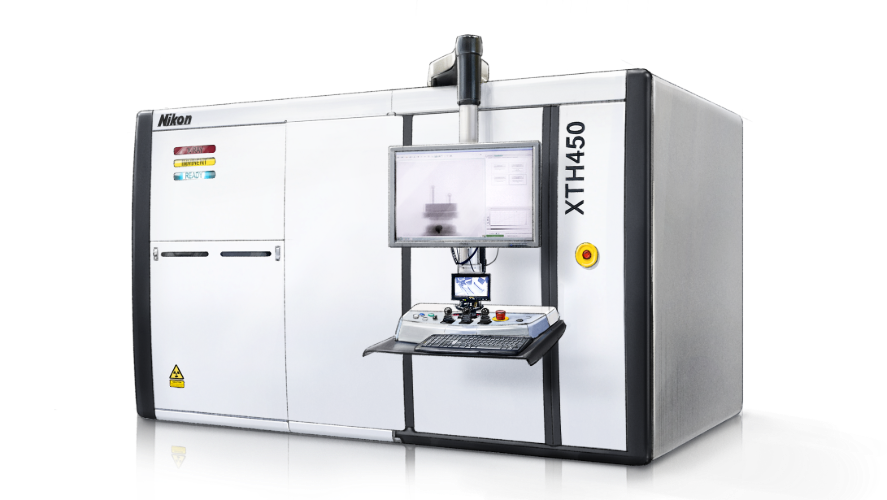
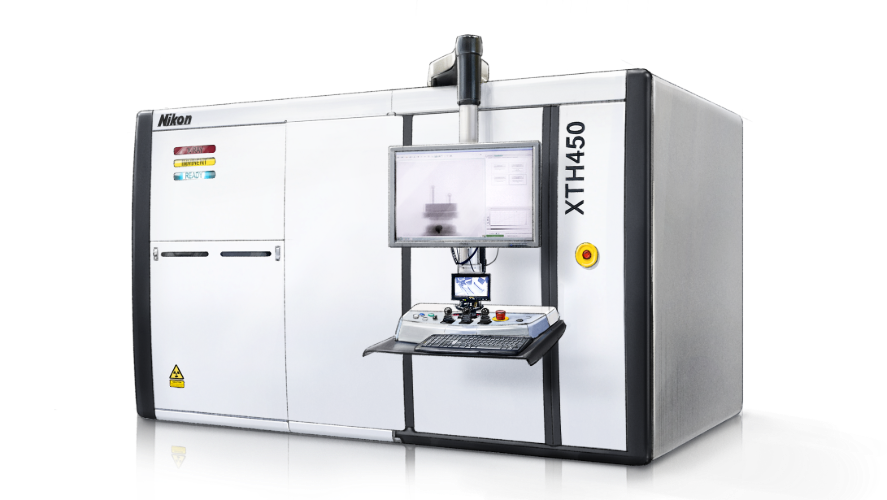
X-RAY CT XT H 450
Model: XT H 450
Brand: Nikon
Origin:
Summary
Unique 450kV microfocus X-ray and CT solution for high-resolution, non-destructive inspection of large and dense components like metal additive manufactured parts, metal alloy turbine blades and large castings.
The unique capabilities offered by Nikon's 450kV/450W microfocus X-ray source enable it to be applied in various fields. Here are a few examples of the potential applications:
1. Industrial Inspection: The high-energy and high-resolution focal spot size make this X-ray source ideal for inspecting dense components in industries such as automotive, aerospace, electronics, and manufacturing. It can help identify defects, cracks, and internal structures within the components.
2. Non-Destructive Testing (NDT): With its ability to penetrate through materials, this technology can be employed in non-destructive testing applications where the inspection of hidden features is necessary. It can be used to assess the integrity of welds, detect internal flaws in structures, and inspect composite materials.
3. Material Science Research: Researchers studying material properties and microstructures can benefit from the high-resolution capabilities of this X-ray source. It allows for detailed analysis of the internal composition and structure of various materials, aiding in the development of new materials and understanding their behavior under different conditions.
4. Art and Cultural Heritage Conservation: This X-ray source can be valuable in the analysis and preservation of artwork and cultural artifacts. It can provide insights into the composition, structure, and condition of delicate objects without causing damage.
5. Medical Imaging: While primarily designed for industrial applications, the high-energy X-rays generated by this source can potentially be utilized in medical imaging for specialized applications where greater penetration is needed, such as imaging dense tissues or large body parts.
These are just a few examples of the potential applications for Nikon's 450kV/450W microfocus X-ray source. Its unique combination of high-energy and high-resolution capabilities opens up possibilities for various fields requiring detailed inspection and analysis.
The high-resolution focal spot size of an X-ray source offers several distinct advantages in inspection and imaging:
1. Increased Detail: A smaller focal spot size allows for finer detail in the captured X-ray images. It provides better spatial resolution, enabling the visualization of smaller features and defects within the inspected object. This level of detail is crucial for identifying and analyzing tiny cracks, voids, or imperfections that might be indicative of structural or material issues.
2. Enhanced Image Clarity: With a smaller focal spot size, the X-ray beam divergence is reduced. This reduction leads to less blurring and scattering of X-rays, resulting in sharper and clearer images. Clearer images make it easier for inspectors to interpret and analyze the internal structures or components being inspected, leading to more accurate and reliable assessments.
3. Improved Measurement Accuracy: High-resolution focal spot sizes contribute to improved measurement accuracy in X-ray inspection. Smaller focal spots provide better localization and precision when measuring the dimensions, distances, and geometrical features of objects within the X-ray images. This is particularly advantageous in industries where precise measurements are critical, such as aerospace, automotive, or electronics.
4. Detection of Smaller Defects: The higher resolution achieved by a smaller focal spot allows for the detection of smaller defects, such as micro-cracks or voids, that may not be visible with a larger focal spot size. This capability is vital for quality control, ensuring that even subtle defects are identified early in the inspection process, thus preventing potential failures or performance issues.
5. Enhanced Capability for Multi-Material Inspections: In cases where multiple materials with differing densities or thicknesses are present in an object, a high-resolution focal spot enables better differentiation between these materials. This enables inspectors to analyze the interfaces and boundaries between different materials more accurately, leading to improved material characterization.
In summary, the distinct advantages of a high-resolution focal spot size include increased detail, enhanced image clarity, improved measurement accuracy, the ability to detect smaller defects, and better differentiation between materials. These advantages collectively contribute to more effective and reliable inspection processes in a variety of applications and industries.
Application
The unique capabilities offered by Nikon's 450kV/450W microfocus X-ray source enable it to be applied in various fields. Here are a few examples of the potential applications:
1. Industrial Inspection: The high-energy and high-resolution focal spot size make this X-ray source ideal for inspecting dense components in industries such as automotive, aerospace, electronics, and manufacturing. It can help identify defects, cracks, and internal structures within the components.
2. Non-Destructive Testing (NDT): With its ability to penetrate through materials, this technology can be employed in non-destructive testing applications where the inspection of hidden features is necessary. It can be used to assess the integrity of welds, detect internal flaws in structures, and inspect composite materials.
3. Material Science Research: Researchers studying material properties and microstructures can benefit from the high-resolution capabilities of this X-ray source. It allows for detailed analysis of the internal composition and structure of various materials, aiding in the development of new materials and understanding their behavior under different conditions.
4. Art and Cultural Heritage Conservation: This X-ray source can be valuable in the analysis and preservation of artwork and cultural artifacts. It can provide insights into the composition, structure, and condition of delicate objects without causing damage.
5. Medical Imaging: While primarily designed for industrial applications, the high-energy X-rays generated by this source can potentially be utilized in medical imaging for specialized applications where greater penetration is needed, such as imaging dense tissues or large body parts.
These are just a few examples of the potential applications for Nikon's 450kV/450W microfocus X-ray source. Its unique combination of high-energy and high-resolution capabilities opens up possibilities for various fields requiring detailed inspection and analysis.
The high-resolution focal spot size of an X-ray source offers several distinct advantages in inspection and imaging:
1. Increased Detail: A smaller focal spot size allows for finer detail in the captured X-ray images. It provides better spatial resolution, enabling the visualization of smaller features and defects within the inspected object. This level of detail is crucial for identifying and analyzing tiny cracks, voids, or imperfections that might be indicative of structural or material issues.
2. Enhanced Image Clarity: With a smaller focal spot size, the X-ray beam divergence is reduced. This reduction leads to less blurring and scattering of X-rays, resulting in sharper and clearer images. Clearer images make it easier for inspectors to interpret and analyze the internal structures or components being inspected, leading to more accurate and reliable assessments.
3. Improved Measurement Accuracy: High-resolution focal spot sizes contribute to improved measurement accuracy in X-ray inspection. Smaller focal spots provide better localization and precision when measuring the dimensions, distances, and geometrical features of objects within the X-ray images. This is particularly advantageous in industries where precise measurements are critical, such as aerospace, automotive, or electronics.
4. Detection of Smaller Defects: The higher resolution achieved by a smaller focal spot allows for the detection of smaller defects, such as micro-cracks or voids, that may not be visible with a larger focal spot size. This capability is vital for quality control, ensuring that even subtle defects are identified early in the inspection process, thus preventing potential failures or performance issues.
5. Enhanced Capability for Multi-Material Inspections: In cases where multiple materials with differing densities or thicknesses are present in an object, a high-resolution focal spot enables better differentiation between these materials. This enables inspectors to analyze the interfaces and boundaries between different materials more accurately, leading to improved material characterization.
In summary, the distinct advantages of a high-resolution focal spot size include increased detail, enhanced image clarity, improved measurement accuracy, the ability to detect smaller defects, and better differentiation between materials. These advantages collectively contribute to more effective and reliable inspection processes in a variety of applications and industries.